在环保政策趋严与“双碳”目标的双重驱动下,污泥处理已成为工业与市政领域的关键战场。数据显示,我国每年产生污泥超6000万吨,其中80%以上含水率超过80%,若直接填埋相当于每年消耗2.4亿立方米土地。如何实现污泥减量化、无害化与资源化?本文将深度解析主流设备技术路线与成本优化策略。在即将开幕的工业节能与环保展上,污泥处理技术也将成为重点关注技术之一。
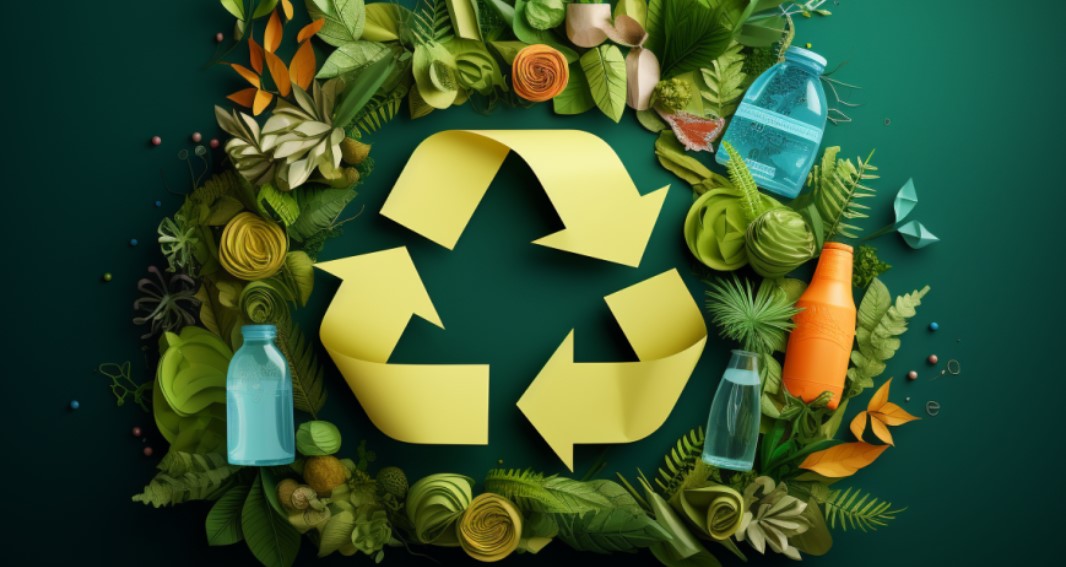
核心挑战:污泥脱水的“三重门”
1. 高含水困局
市政污泥含水率普遍在80%-99%,运输与处置成本高昂。以日处理10万吨的污水厂为例,若污泥含水率从99%降至60%,体积可减少83%,年节省运费超500万元。
2. 成分复杂性
污泥中富含重金属、病原体及有机污染物,传统填埋易引发土壤与地下水二次污染。欧盟已明确要求填埋污泥有机质含量低于5%,倒逼脱水技术升级。
3. 资源化瓶颈
脱水后的污泥需满足特定指标方可资源化利用:焚烧要求含水率<50%,制建材需重金属达标,堆肥则要求有机质>40%。
技术破局:脱水设备的“五虎将”
1. 板框式高压压滤机
原理:通过液压系统施加15-25bar压力,使污泥在滤布间挤压成型。
优势:出泥含水率低(可达50%),适用于高粘度工业污泥。
短板:间歇式作业,自动化程度低,人工成本占比高达30%。
2. 带式连续压滤系统
创新点:多层滤带重力脱水+辊压脱水,支持24小时连续运行。
适用场景:市政污水厂大规模处理,单机日处理量可达200吨。
局限:对絮凝剂依赖度高,药剂成本占运营费用40%-60%。
3. 离心脱水机
技术亮点:利用3000-4000G离心力实现泥水分离,无需滤布。
效率对比:处理活性污泥时,含水率可比带式压滤降低8%-10%。
经济性:电耗较高,适用于含油污泥等高附加值场景。
4. 隔膜压榨机
二次压榨:在普通压滤后,用弹性隔膜二次加压至30bar,含水率可降至45%以下。
案例:某化工厂采用该设备后,污泥热值提升至1500kcal/kg,满足掺烧发电要求。
5. 电渗透深度脱水
前沿技术:施加直流电场破坏污泥胶体结构,结合机械压滤使含水率突破40%大关。
成本:设备投资是传统设备的2-3倍,但可节省30%药剂费用。
成本密码:从吨处理费到全生命周期优化
1. 直接成本拆解
药剂成本:聚丙烯酰胺(PAM)添加量通常为污泥干重的0.2%-0.5%,单价波动大(1.5-3万元/吨)。
能耗对比:离心机(3-5kWh/t)>带式压滤(1.5-2.5kWh/t)>板框压滤(0.8-1.2kWh/t)。
人工维护:自动化设备可减少60%人力投入,但智能控制系统需增加15%-20%初期投资。
2. 选型黄金法则
工业污泥:优先选择耐腐蚀的钛合金板框压滤机,应对酸碱环境。
市政污泥:带式压滤+化学调质组合性价比最高,吨处理成本约80-120元。
应急处理:撬装式离心脱水机组可快速部署,适用于临时性项目。
3. 隐性成本警示
滤布损耗:板框压滤机年均更换滤布费用达设备价的10%-15%。
环保风险:未达标污泥外运可能面临10-100万元/次的行政处罚。
未来趋势:从脱水到资源化的技术融合
1. 热解气化技术
将含水率30%的污泥在无氧条件下热解,产出可燃气体(热值12-15MJ/m³)与生物炭,碳减排率超60%。
2. 微生物破壁技术
利用嗜热菌分解污泥细胞壁,释放结合水,可使后续脱水能耗降低40%。
3. 物联网智能运维
通过传感器实时监测污泥比阻、药剂投加量,AI算法自动优化运行参数,设备综合效率(OEE)提升25%以上。
结语
污泥处理已从“成本负担”转向“资源金矿”。选择适配工艺、挖掘降本空间、布局资源化技术,将成为企业绿色转型的核心竞争力。当每一吨污泥都能转化为能源或材料,环保与效益的共赢图景便不再遥远。